
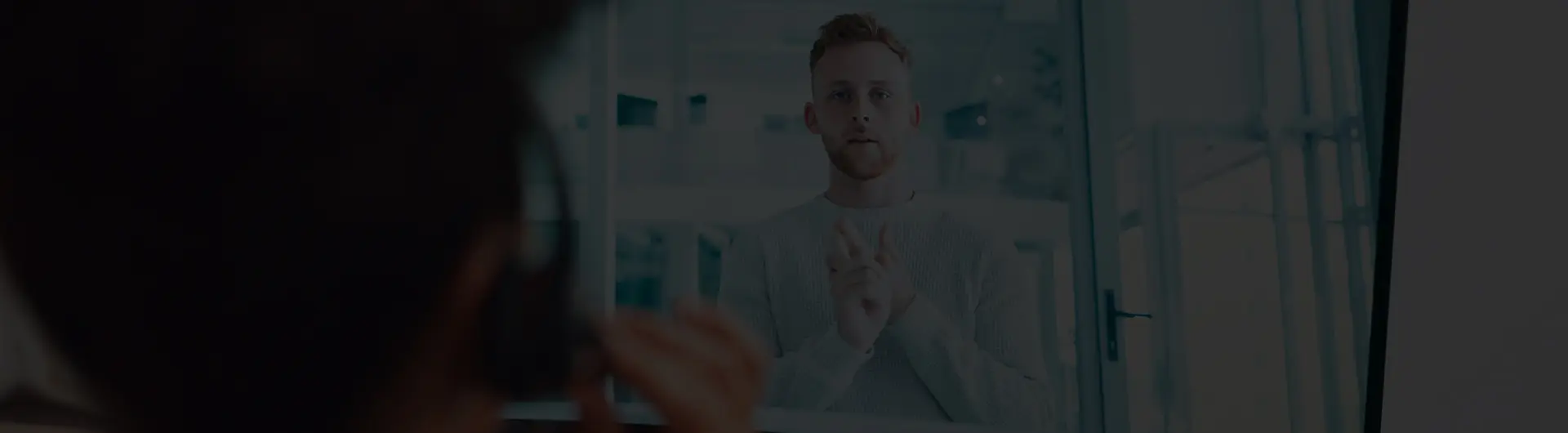
Overcoming Industry Standards: How to Choose the Best Compression Load Cell Amidst Common Challenges
In the realm of industrial weighing solutions, the selection of a Compression Load Cell is often overshadowed by prevailing industry standards that emphasize uniformity and compliance over innovation and performance. According to a recent market analysis report by Research and Markets, the global load cell market is expected to reach USD 4.4 billion by 2025, highlighting the growing demand for precise and reliable measurement tools across various sectors. As industries evolve, the challenges of choosing the best Compression Load Cell become more apparent, including issues of sensitivity, environmental factors, and integration with existing systems. This blog aims to explore the intricacies of navigating industry standards while illuminating the pathways to selecting the optimal Compression Load Cell that not only meets compliance but also enhances operational efficacy.
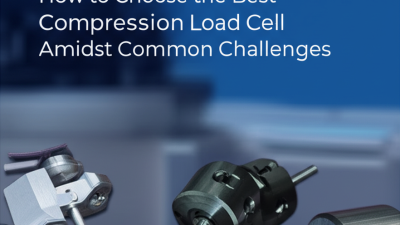
Identifying Key Factors in Load Cell Selection for Your Industry Needs
Choosing the right compression load cell is essential for maximizing operational efficiency and ensuring accurate measurements across various industries. When selecting a load cell, several key factors must be considered, including precision, capacity, and environmental conditions. According to a report by MarketsandMarkets, the global load cell market is expected to grow from $2.40 billion in 2020 to $3.53 billion by 2025, reflecting the critical role these devices play in industrial applications. For instance, industries requiring high capacity and accuracy, such as aerospace and automotive, often need load cells that can handle extreme conditions without compromising performance.
Additionally, it is crucial to evaluate calibration options and the load cell’s compatibility with existing systems. A study published by ResearchAndMarkets highlights that approximately 18% of load cell failures are due to incorrect calibration, leading to significant financial losses and operational downtime. Selecting a load cell with flexible calibration capabilities can mitigate these risks. Furthermore, understanding the specific environmental factors such as temperature and humidity can help in choosing a load cell that is not only robust but also reliable for long-term use, ensuring that the chosen device meets the specific demands of the industry while upholding rigorous standards.
Understanding Common Challenges in Compression Load Cells
When selecting a compression load cell, industry professionals often face several common challenges that can complicate the decision-making process. One significant hurdle is understanding the specific application requirements. Compression load cells are used in various settings, each with distinct environmental conditions and operational demands. This requires a careful assessment of factors like load capacity, accuracy, and environmental factors such as temperature and humidity, which can all impact performance.
Another prevalent challenge is navigating the vast array of available technology and specifications. With advancements in load cell design and manufacturing, it can be difficult for engineers and quality managers to determine which models offer the best reliability and precision for their needs. Additionally, compatibility with existing equipment and systems is an important consideration; improper integration can lead to inaccurate readings or equipment failure. To overcome these challenges, it’s crucial to thoroughly evaluate supplier options, seeking out those who provide comprehensive support and testing to ensure optimal functionality.
Comparative Analysis: Domestic vs. International Load Cell Manufacturers
When selecting a compression load cell, understanding the landscape of domestic versus international manufacturers is crucial. According to the latest market analysis by Grand View Research, the global load cell market is expected to reach USD 2.5 billion by 2025, driven by the increasing demand for accurate measurement in various industries. Domestic manufacturers often offer faster response times and better customer support, while international suppliers might provide advanced technology and broader product variety. For example, while domestic brands like Omega Engineering are popular for their reliability, international companies such as Flintec are known for their innovative features and precision.
**Tip:** When assessing load cell manufacturers, prioritize those compliant with industry standards such as ISO 9001. This ensures that their products meet essential quality benchmarks, enhancing your operational efficiency.
Moreover, it’s essential to consider the cost-benefit ratio. Domestic manufacturers might have lower initial costs, but international brands may provide longer warranties and specialized performance that can justify a higher upfront investment. A report from ResearchAndMarkets indicates that precision in load measurement directly influences production line efficiency by up to 20%, emphasizing the importance of making an informed choice.
**Tip:** Explore manufacturers that offer trial periods or have a robust return policy. This allows you to evaluate the load cell's performance in real-world applications before committing long-term.
Innovative Solutions for Enhanced Load Cell Performance
Choosing the right compression load cell can be daunting due to the myriad of options available and the common challenges faced in the industry. Innovative solutions play a crucial role in enhancing load cell performance, ensuring that users achieve accurate and reliable measurements under various conditions. For instance, advancements in materials and design have led to load cells that offer better durability and resistance to environmental factors such as humidity, temperature fluctuations, and mechanical shocks.
Additionally, the integration of smart technology into load cell systems has revolutionized how data is processed and utilized. Modern load cells equipped with IoT capabilities allow for real-time monitoring and data analysis, providing users with valuable insights into load behaviors. This not only improves operational efficiency but also aids in predictive maintenance, reducing downtime and extending the lifespan of the equipment. By focusing on these innovative solutions, industries can overcome traditional limitations and select the most effective compression load cell for their specific applications, driving performance and reliability to new heights.
Building Trust: The Importance of Quality Assurance in Load Cell Production
Quality assurance is a cornerstone of load cell production, especially when selecting the best compression load cell in a competitive market. The importance of maintaining high standards cannot be overstated, as it directly impacts the performance, reliability, and longevity of these critical components. A robust quality assurance process involves meticulous testing and validation at every stage, from material selection to final inspection. This ensures that each load cell meets or exceeds industry specifications and can withstand the rigors of real-world applications.
Moreover, building trust with customers hinges on transparent quality assurance practices. When manufacturers openly share their testing protocols and quality certifications, they foster confidence in their products. Customers are more likely to choose a supplier that demonstrates a commitment to excellence, knowing that their load cells are engineered with precision and reliability in mind. In an industry where accuracy is paramount, a solid quality assurance framework not only enhances a brand's reputation but also facilitates long-term customer loyalty and satisfaction.