
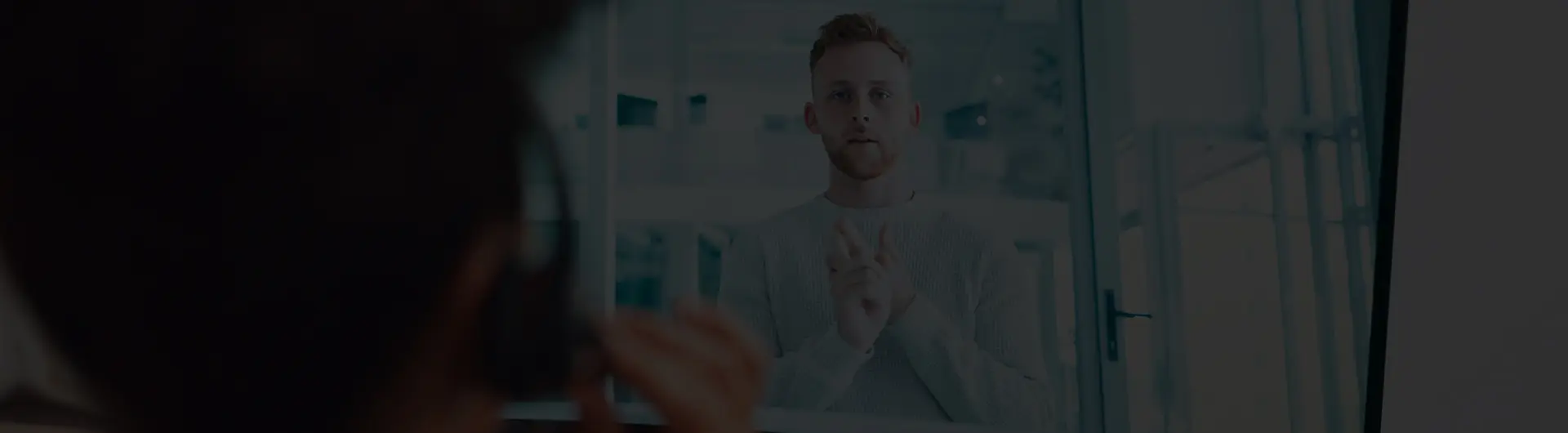
10 Compelling Reasons to Choose Force Sensors for Your Next Project
In recent years, the demand for precise measurement technology has surged, driving innovation in various industrial sectors. Force sensors, integral to applications ranging from robotics to automotive testing, are at the forefront of this transformation. According to a report by MarketsandMarkets, the global force sensor market is projected to grow from USD 2.21 billion in 2020 to USD 3.84 billion by 2025, reflecting a compound annual growth rate (CAGR) of 11.4%. This growth underscores the increasing reliance on force sensors for applications that require meticulous force measurements and feedback systems. As industries strive for enhanced automation and quality control, choosing the right force sensor can pave the way for more efficient, reliable, and innovative project outcomes. In this blog, we will explore ten compelling reasons to integrate force sensors into your next project, highlighting their crucial role in modern technology and engineering.
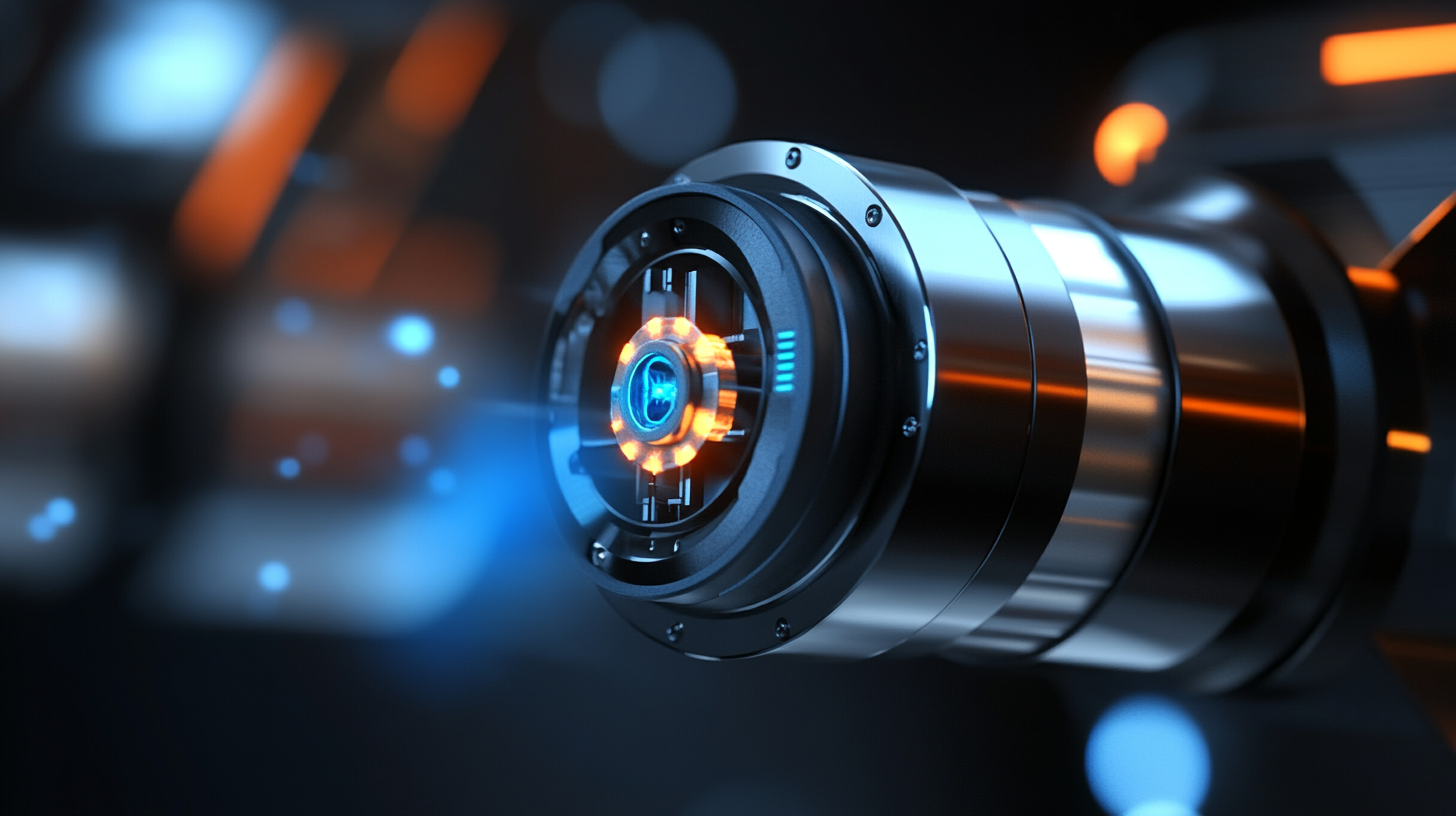
Benefits of Enhanced Precision in Measurement with Force Sensors
Force sensors are essential tools in the realm of precision measurement, enabling projects to achieve heightened accuracy and reliability. The ability to measure force with exceptional precision allows engineers and designers to gather critical data that can refine their prototypes and final products. Whether it's in automotive applications, robotics, or medical devices, the accuracy provided by force sensors can significantly impact performance and safety outcomes.
Enhanced precision in force measurement leads to improved product quality. With the implementation of force sensors, minute variations in force can be detected, allowing for better control during manufacturing processes. This not only minimizes errors and waste but also ensures that end products meet strict quality standards. Moreover, precise force measurements can contribute to smarter designs where forces are optimized, resulting in innovative solutions that push the boundaries of what is possible in technology and engineering.

Versatility of Force Sensors Across Various Industries
Force sensors are becoming an indispensable tool across various industries due to their remarkable versatility. In manufacturing, they play a crucial role in quality control processes, helping to ensure products meet necessary specifications by accurately measuring force and pressure during production. This capability enhances operational efficiency and minimizes waste, making force sensors a sought-after asset for manufacturers looking to optimize their output.
In the healthcare sector, force sensors find their applications in robotic surgery and rehabilitation devices. These sensors enable precise measurements of forces exerted during medical procedures, ensuring patient safety and improving surgical outcomes. Moreover, in fields like sports technology, force sensors are used in wearable devices to track athletes' performance by measuring the forces involved during movements. This information helps in developing training programs tailored to individual needs, showcasing the all-encompassing nature of force sensors in enhancing performance across various domains.
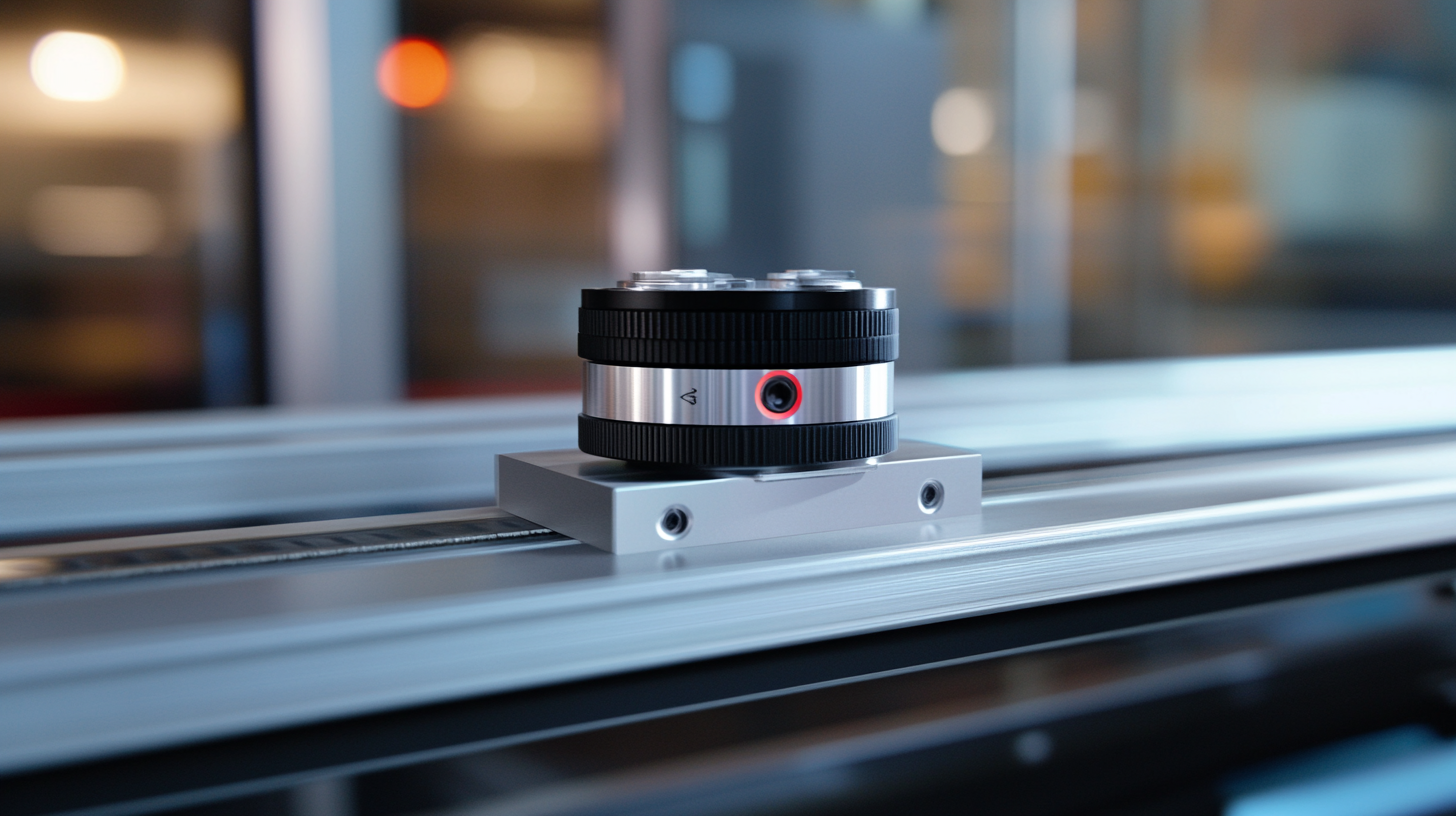
Cost-Effectiveness and Efficiency Boosts Using Force Sensors
In today’s competitive landscape, cost-effectiveness and efficiency are paramount for project success, and integrating force sensors can significantly enhance both. According to a report by ResearchAndMarkets, the global force sensor market is projected to grow at a CAGR of 10.2% from 2021 to 2026, reflecting a robust demand across various sectors, including automotive, healthcare, and robotics. This growth underscores the increasing recognition of force sensors as essential tools for optimizing operational performance.
Utilizing force sensors not only reduces costs associated with manual input and error corrections but also improves overall project efficiency. A case study published by the International Journal of Advanced Manufacturing Technology highlights that integrating force sensors in automated assembly lines led to a 30% reduction in production time and a 20% decrease in material waste. These metrics demonstrate that the implementation of such technology can yield significant savings and enhance productivity, making force sensors a compelling choice for any innovative project.
Distribution of Benefits from Force Sensors
Improved Safety Features Enabled by Force Sensor Technology
Force sensor technology has emerged as a pivotal advancement in enhancing safety across various industries. According to a recent report by the International Society of Automation, the integration of force sensors in manufacturing processes has led to a significant reduction in workplace injuries, with statistics indicating a decrease of up to 25% in related incidents. This improvement can largely be attributed to the sensors' ability to monitor and respond to applied forces in real time, enabling more precise control of machinery and tools.
Moreover, sectors such as automotive and healthcare are reaping the benefits of force sensors to bolster safety protocols. In the automotive industry, employing force sensors in collision detection systems has been shown to improve reaction times, potentially reducing the severity of accidents by as much as 30%. In healthcare, force sensors aid in patient monitoring, ensuring that the applied pressure during treatments or surgeries remains within safe limits, thereby minimizing the risk of injury. The data underscores the transformative role of force sensors in creating safer environments, inviting more industries to adopt this innovative technology.
Reason | Description | Benefits |
---|---|---|
1. Enhanced Safety | Force sensors can detect excessive loads and prevent equipment failure. | Reduces risk of accidents and injuries in the workplace. |
2. Real-time Monitoring | Provides instant feedback on force, allowing for immediate adjustments. | Improves operational efficiency and responsiveness. |
3. Versatile Applications | Can be used in various industries like automotive, robotics, and healthcare. | Flexible solutions for diverse engineering challenges. |
4. Energy Efficiency | Helps optimize energy use by monitoring load conditions. | Reduces operational costs through better resource management. |
5. Data Collection | Collects valuable data that can be analyzed for trends. | Enables informed decision-making and predictions. |
6. Improved Product Design | Allows engineers to refine designs based on real force measurements. | Creates safer, more efficient products. |
7. Cost-Effective | Reduces the need for expensive safety measures and design changes. | Saves money in project development. |
8. Easy Integration | Can be easily implemented into existing systems. | Minimizes disruption during deployment. |
9. Scalability | Suitable for projects of all sizes, from small prototypes to large installations. | Offers flexibility as project needs grow. |
10. Enhanced User Experience | Provides direct feedback to users, improving interaction with devices. | Increases user satisfaction and trust in the technology. |
Integration Ease of Force Sensors in Modern Projects
Force sensors have gained popularity in modern projects due to their unparalleled integration ease, providing engineers and designers with a seamless way to enhance functionality and performance. One of the primary advantages of force sensors is their versatility; they can be easily incorporated into various applications, from robotics to consumer electronics. The compact form factor of many force sensors allows for straightforward embedding within limited spaces, thus simplifying design considerations without compromising overall system integrity.
Additionally, the rapid development of digital interfaces and wireless communication protocols further facilitates the integration of force sensors into existing systems. This interoperability means that developers can implement these sensors without major overhauls, allowing for quick prototyping and faster time to market. Moreover, the support of various software platforms simplifies data acquisition and processing, providing a user-friendly experience for engineers who may not have extensive experience with sensor technologies. The ability to gather and analyze real-time data can lead to informed decision-making, ultimately enhancing the competitiveness of any project.